Today, airlines in the world use brush plating process for maintenance and overhaul of select aircraft components. Furthermore, the majority of the military air forces and naval air crafts around the world finds it valuable.
Sterling assists in repairing components or dealing with production work. We offer training to allow your employees to do the necessary brush plating using LOPSCO Brush Plating Process or have one of our certified technicians to do the work for you. Below are some of the examples of our applications:
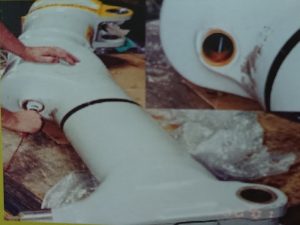
Cadmium Plating on Landing gear components QQ-P416F
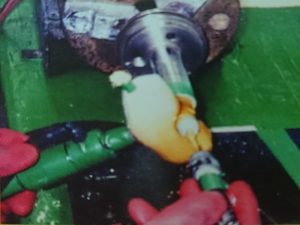
With minimum masking involved, plating is concentrated where you need it without affecting the surrounding plating
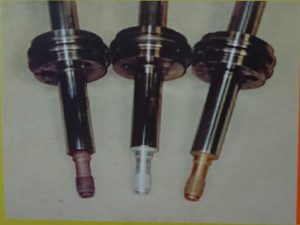
Plating threads on a damper piston rod. Picture showing from left to right 3 damper piston thread before plating, after cadmium coating and after the type II coating.
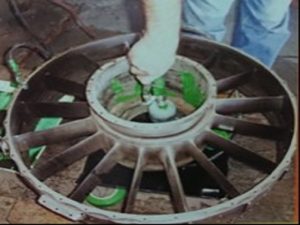
Nickel Plating to repair the diameter of a turbine. Anodize repairs can be done to MIL-A-8625 Type I and II without affecting the existing anodic coating.
A single trained technician can perform a vast variety of plating operations.
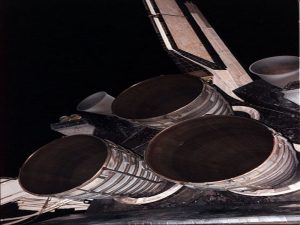
Space Shuttle Main Exhaust Nozzle requires nickel plating for brazing to take place.
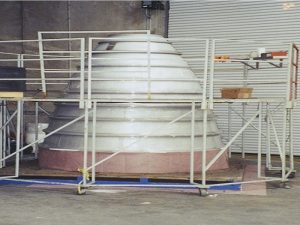
Preparing for brush plating.
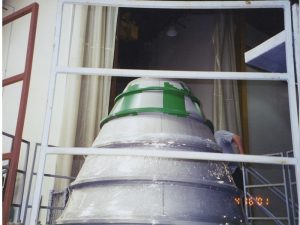
The close up look at the ring one and ring two of the exhaust nozzle. The picture shows the initial stages of masking on the exhaust nozzle.
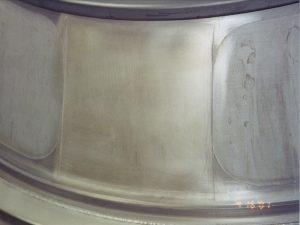
Nickel Brush Plating is completed on the exhaust nozzle.
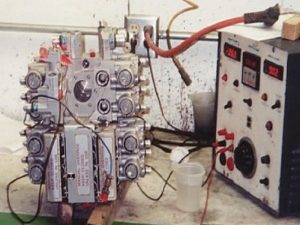
Damaged Valve Assembly. The damaged ID anodic coating is being removed from one of the port. Then using brush plating anodizing solution, the ID was selectively repaired.
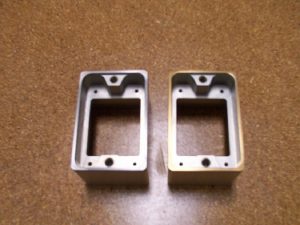
Missile System – Connection Box. Gold Plating on an aluminum housing is required to ensure an electrical connection is maintained for long periods for missile operations.
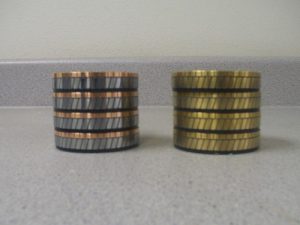
Missile System – Commutator Stacks. Commutators are used in various missiles and the gold is to prevent corrosion and to ensure electrical conductivity.
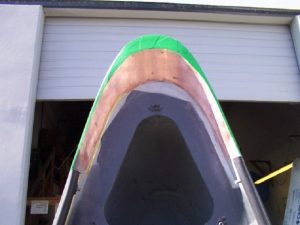
Antenna Assembly of KC – 35 Refueling Tanker. This antenna which is copper requires silver for better performance