LOPSCO Brush plating process save time and reduce costs when repairing damaged cylinders.
SAVE TIME and COST: Conventional ways of cylinder repair takes at least 21 days. Our Repair is time efficient using only 3 to 4 days to restore the cylinder back to the original printing condition. Repair is done in-situ and disassembly is not required. Expensive downtime cost is saved.
Heideberg Printing Cylinder
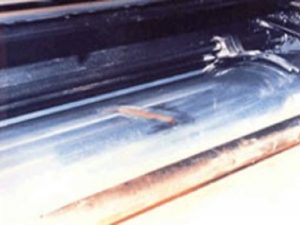
A Heidelberg Printing Machine with an Indentation filled with copper plating.
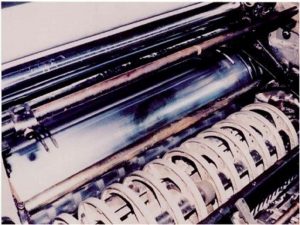
The Heidelberg Printing Machine Capped with Nickel to restore cylinder to origin surface condition.
Man Roland Printing Cylinder
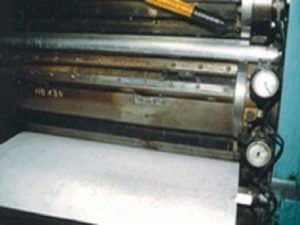
A Man Roland RFK-3B, with a chipped edge on the Upper Blanket cylinder. After repairing the chipped edge with a metal-cladding process. LOPSCO Brush Plating Process was utilized to complete the repair.
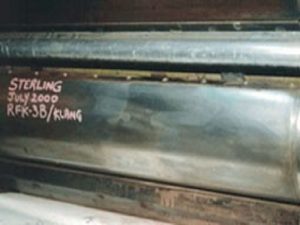
The Man Roland RFK-3B cylinder after LOPSCO Brush Nickel Plating process.
Ryobi Printing Cylinder
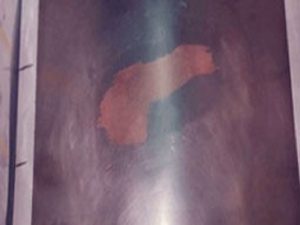
LOPSCO Brush plating process was utilized to repair the low patch impression area on a Ryobi offset cylinder.
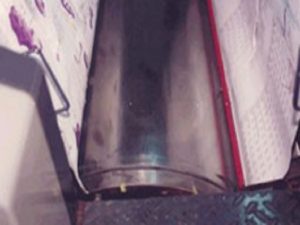
The RYOBI Cylinder after LOPSCO Brush Nickel plating.
Heideberg Printing Cylinder
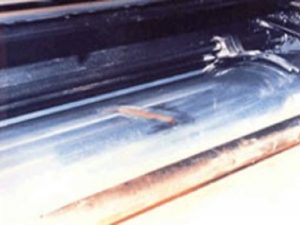
A Heidelberg Printing Machine with an Indentation filled with copper plating.
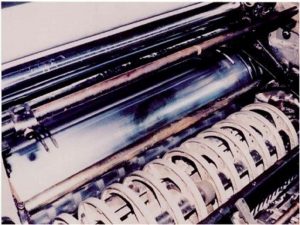
The Heidelberg Printing Machine Capped with Nickel to restore cylinder to origin surface condition.
Man Roland Printing Cylinder
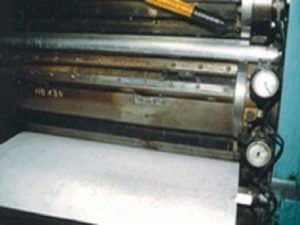
A Man Roland RFK-3B, with a chipped edge on the Upper Blanket cylinder. After repairing the chipped edge with a metal-cladding process. LOPSCO Brush Plating Process was utilized to complete the repair.
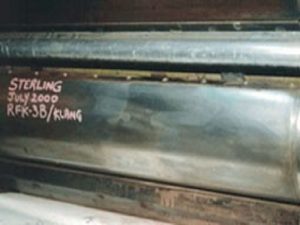
The Man Roland RFK-3B cylinder after LOPSCO Brush Nickel Plating process.
Ryobi Printing Cylinder
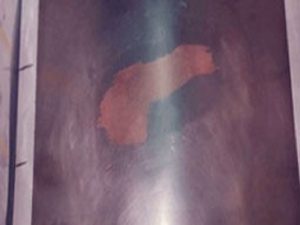
LOPSCO Brush plating process was utilized to repair the low patch impression area on a Ryobi offset cylinder.
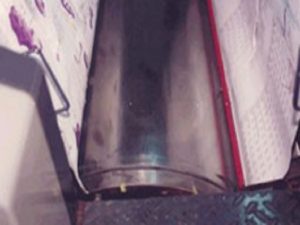
The RYOBI Cylinder after LOPSCO Brush Nickel plating.